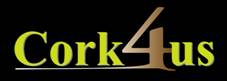
History of Cork
by Joaquim Loureiro at
Cork4us
Part 1.
Cork
is the bark of cork oak (Quercus Suber L), a noble tree with
very special characteristics that grows in Mediterranean regions
such as Spain, Italy, France, Morocco, Algeria, and especially
Portugal, where there are more than 720 000 hectares of cork oak
forests, as well as a cork industry of great economic
importance.
It is an astonishing
tree of great longevity and a great capacity for regeneration.
It can live on average 150 to 200 years, despite the many
harvests that make throughout his life: about 16 interspersed
with periods of nine years.
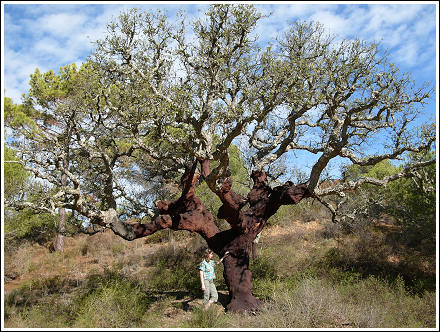
Quercus suber from Algarve,
Portugal
Photo by Hannes Grobe © 2004
This plant tissue which
is harvested as carefully - cork - has unique qualities, unique
and to date no human ingenuity could mimic or exceed:
1. Very light
2. Impermeable to liquids and gases
3. Elastic and compressible
4. An excellent thermal and acoustic
5. Smouldering
6. Very resistant to abrasion
But it is, above all,
one hundred percent natural materials, recyclable and
biodegradable, essential qualities in a society like the current
you want less polluted and environmentally friendly.
Despite its many uses,
for centuries the most faithful ambassador of cork stoppers in
the world is natural, this seal of exceptional quality still
preferred and demanded by the major wine producers. But
throughout history, there are many references to this product
and its varied applications. In 3000 BC, the cork has been in
use in China, Egypt, Babylon and Persia for the manufacture of
fishing tackle. In Italy we found remains dating from the fourth
century BC, include artefacts such as floats, stoppers for
casks, women's shoes and roofing materials. It is also this time
we have one of the first references to the cork oak, by the
Greek philosopher Theophrastus, in his botanical treatises, he
says, amazed, "the faculty that this tree has to renew its bark
after it is removed."
Even in the Roman Empire
44 a.C, the troops were the shields of protection in Cork due to
its strength and lightness of this wonderful natural product.
Portugal can boast of
having been a pioneer in environmental legislation, as the early
agrarian laws protecting cork forests appear at the beginning of
the thirteenth century, in 1209. Later, during the Discoveries,
the builders of ships and Portuguese caravels that set out to
discover new worlds used oak wood in the manufacture of parts
exposed to the elements. They argued that the "thrash" as it was
then called, was what was best for the bond of the ships, as
well as strong, it never rotted.
The life cycle of the cork as a
raw material begins with the extraction of the cork bark, called
stripping, which takes place during the most active growth of
the cork, between mid-May or early June to late August.
But few know that it
takes 25 years until the trunk of a cork oak begins to produce
and be profitable. Each trunk has to reach a circumference of
about 70 cm when measured at 1.5 meters from the ground. Since
then, its operation will last 150 years on average.
The first stripping,
Desbois the call, you get a cork very irregular structure with a
hardness that makes it difficult to work. It's called virgin
cork to be used in applications other than corks (flooring,
insulation etc.), because it is far from presenting the quality
needed for this purpose.
Nine years later, the
second harvest, we obtain a material with a regular structure,
less hard, but still not suitable for the manufacture of corks
and so-called secondary cork.
It is only in the third
and subsequent harvests, you get the cork with the appropriate
properties for the production of cork stoppers and discs of
quality, since it already has a regular structure with smooth
back and tummy. It's called cork amadia or reproduction. From
this point, the cork will provide, for nine years, cork with
good quality for about a century and a half, producing an
average of 15 to 16 harvests throughout his life. But how do you
take off the cork tree?
The stripping of the
cork oak is an ancient process that can only be done by
specialists, the debarkers as not to harm the tree, it should be
much manual skill and experience. And it consists of five steps:
First strike is the cork
in the vertical direction, choosing the deepest crack the shell.
At the same time, twist the ax to separate the inner bark. Then
separate the board with the introduction of the hatchet between
the board and the inner bark of belly. Then, you run a twisting
movement of the hatchet between the trunk and the cork strip to
be separate. With a horizontal cut defines the size of the board
of cork is removed and what the tree. Board is then carefully
removed from the tree not to leave. The larger planks extracted,
the greater its market value. It is the skill of debarkers that
allows to obtain the entire board. Withdrawal first board, these
operations are repeated for the whole trunk. After extraction of
the boards, remains adherent fragments of cork at the base of
the trunk. To remove any parasites that exist in cork shims, the
harvesting gives a few blows with the ax.
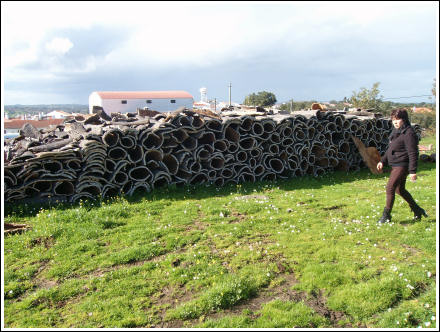
Harvested bark from cork oak.
Finally, mark up the
tree, using the last number of years in which the extraction
took place.
So we could say that you
could already make the discs called the magnificent flower to
fishing rods, but there is still a long way before it can make
that object. After removal of the mortar so desired, the cork
planks are stacked or the forest or on construction sites within
the premises of a factory. There they remain exposed outdoors,
the sun and rain. However, all batteries are constructed taking
into account its own rules and very strict in order to allow the
stabilization of the cork. They must be stacked on materials
that do not contaminate the cork and prevent contact with soil.
Wood, for example, is expressly prohibited because it can
transmit fungi. During this period of rest gives the maturation
of the raw material and cork stabilizes. Since this period of
rest of the boards of no less than six months.
After six months of
stabilization of the cork, this is cooked in boiling water for
one hour, and after boiling the cork back to rest for 3 weeks to
get the consistency needed for its transformation into stoppers,
discs, skin, etc..
It is never too often
repeated that the cork is a natural, recyclable and reusable. To
take advantage of and preserve this valuable resource, a growing
number of countries have made efforts to carry out recycling
initiatives in order to raise awareness among local people for
the wealth of material.
Although recycled cork
is never reused to produce corks for wines or disks for fishing
rods, there are many other possible alternative applications.
For example, bulletin boards, bookmarks, coasters, flooring or
insulation material.
So my friends or
Rodmakers Rodbuilders never forget that each cork disc they pass
through the hands are the fruit of a tree with a minimum of 50
years, and that the cork disc has 9 years of growth.
End of part 1.
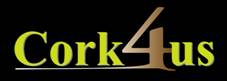
Cork story Part 2
In order to know that each disk
has a minimum of nine years and the tree has at least 50 years,
it should be necessary said how the cork is choosed as well as
the pores are defined of this precious natural product. All cork
has pores and cork without pores doesn't exist. So was rated all
kind of pores and finer pores are needle pores and open pores
are partridge eye pores.
The choice of cork translates
into six qualities which translates into cork 1st, 2nd, 3rd,
4th, 5th and 6th. In qualities 1st and 2nd is where to find the
quality TOP FLOR , FLOR and EXTRA, but how the name FLOR appear
in a cork? When you make the choice on a cork board and that
shows a smooth surface with few pores and these pores are the
pores called needle pore, all the people who work with cork have
the habit of saying (cork is so beautiful that it seems a
flower), this phrase has always said that was named to call FLOR
at all cork of excellent quality.
The cork 3rd quality is where
is extracted discs with quality SUPERIOR AAA and quality A, the
remaining ratings these are normally used for grinding and
becomes granulated cork which in turn give rise to insulation
boards, floor of cork, agglomerate stoppers for wine, etc.
In relation at thick at the
cork board, i read that cork board grows by 1,5mm every year, as
this situation is not 100% true but is nonetheless true. There
are trees with the cork harvested after nine years (can’t be
extracted with less age), has a thickness of 10mm and there are
cork trees that give thicknesses of 55mm. Thus was created a
classification with standard measures of cork which became known
as the following: Cork with thicknesses between 4 and 6 rows are
given the name of DELGADINHOS Cork with thicknesses between 7
and 12 rows are given the name of SLENDER (DELGADOS) Cork
thicknesses exceeding 12 lines gives the name HALF MARK, MARK
and TRIANGLE and each row is 2,6mm
But then, how produce a disc of
cork?
After choosing the right cork
that will transform this already and of course, have been cooked
and stay in home for stabilization, then begins the process of
transformation.
The first step is to cut the
board into strips with the same width and this process we call
STRIPPING (image 2).
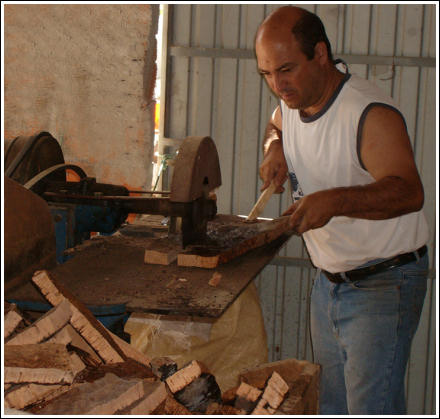
(1)
As the disc is produced in
reverse at the stopper, the disc is done vertically while the
stopper is done horizontally, we spent for the second and third
step is to remove the belly and the coast of cork (image 2). In
this process we call LAMINATION.
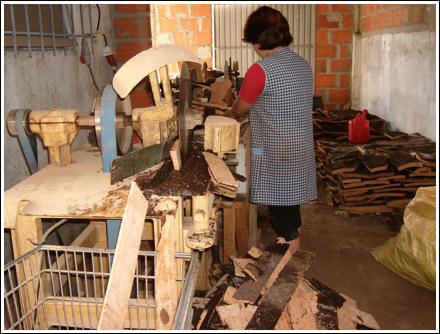
(2)
In accordance with laminated
french toast pass to the process of drilling or drilling discs.
The discs can be made in manual or automatic machines, which
exist points for and points against. While working with manual
machine, the worker can always choose the better part of toast
for removing a disc with more quality which does not happen with
the automatic machine for producing of discs, because don't make
any kind of choice. The strong point of the automatic machine is
the amount that can be produced during the workday that is much
larger than the manual machine (image 3).
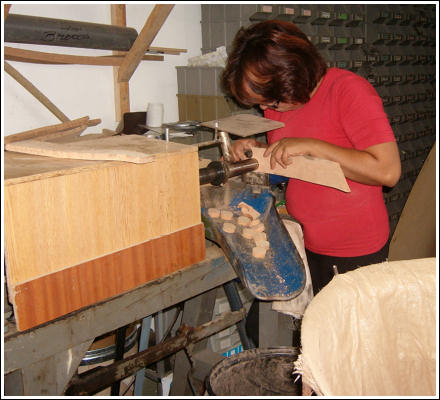
(3)
Due to these production points
very important, CORK4US applied to the manual process of cork
production for the qualities 1st to 3rd, because to obtain a
good quality disc has to choose well where it will drill. Once
you get this disc, usually has a diameter higher than the normal
to send to customers, which is now headed for the calibration
process for this disc and all discs go through a machine that
will calibrate placing the correct measure desired by customers.
in this process we call demote (image 4).
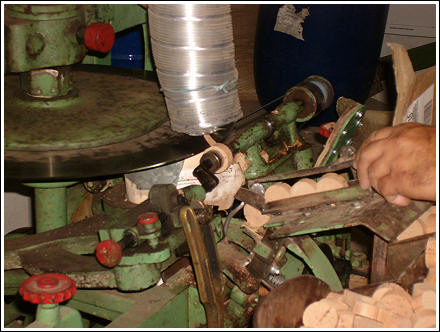
(4)
The demoted is a machine that,
by decreasing the diameter of the disc puts the simultaneously
the round face with a perfect finish beautiful, and removing any
angle so that it is not intended to disk. Right now it has
reached the end of production of the disc is time to choose the
qualities.
In choosing is where removes
any disc that appears to be faulty and selects all the
qualities, and such discs are on a treadmill which is in
constant two people to select the disks. Finished in a selection
carpet is then made the manual accurate choice to obtain all the
desired qualities (image 5).
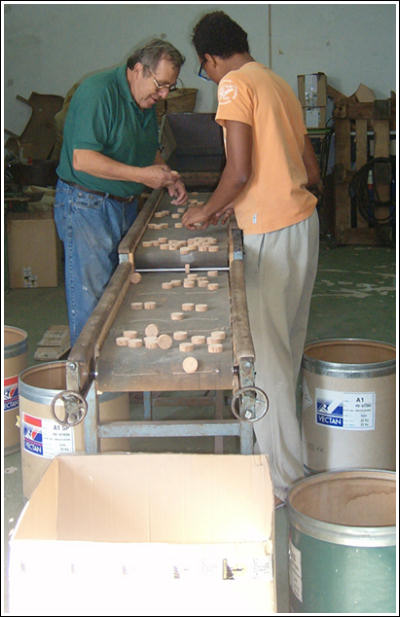
(5)
The discs selected in their
respective graduations are: TOP FLOR ; FLOR ; EXTRA ; SUPERIOR
AAA ; A and B. The process of center hole can be done if the
customer desire (image 6).
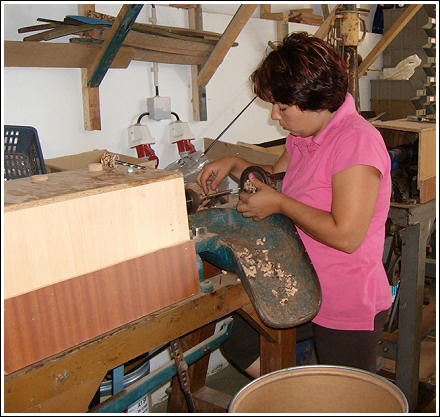
(6)
The final step is to pack and
ship to customers anywhere in the world
CORK4US team is proud to inform
all rod builders and rod makers that all discs are thoroughly
revised so that there aren't gaps in quality. The satisfaction
of our customers has been elevated, to whom we give our thanks
for the trust delivered. our webpage is
www.cork4us.com and can
be view all quality cork discs produced in our factory.
Written by
Joaquim Loureiro 2013 ©
www.cork4us.com
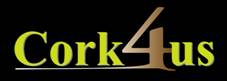 |